Cheap, strong and versatile, concrete is the second most consumed material globally after water, with 30 billion tonnes used annually (Nature 597, 593–594; 2021). Production of concrete is energy intensive and is responsible for more than 7% of anthropogenic carbon dioxide emissions — of which cement accounts for the vast majority.
Extraction of the minerals and other materials used to make concrete is also environmentally unfriendly. For example, around 50 billion tonnes of sand and gravel1, and more than 5 billion tonnes of limestone are mined annually, resulting in habitat loss, soil erosion and pollution. These impacts will only worsen, as the global market for concrete continues to grow.
The construction industry needs to become more sustainable by minimizing carbon emissions and reducing resource and energy use2. Such a vision was set out, in part, in 2023 at the United Nations climate summit in Dubai through the Cement and Concrete Breakthrough Initiative. Launched by 45 world leaders, this initiative aims to reduce the emissions associated with producing one tonne of cement by around 20% by 2030, compared with 2020 levels. Strategies include increasing the use of alternative fuels and other cement-like materials, using construction materials more efficiently, and implementing carbon capture and storage.
Reducing emissions is achievable. But a more comprehensive strategy for sustainable concrete is also needed, with the ultimate goals of net-zero carbon emissions and use of 100% recycled materials (see ‘Steps to net-zero concrete). Here we set out the key ingredients of a ‘net zero concrete’ strategy.
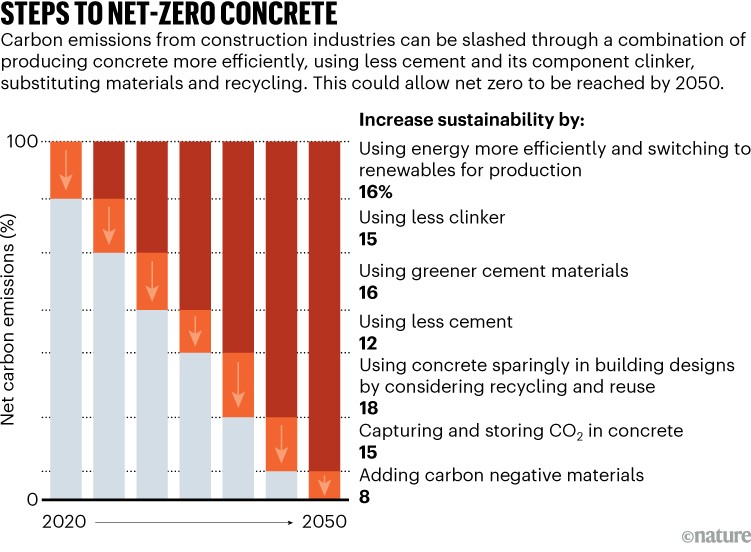
Source: Analysis by J. Xiao et al.
Design more efficient kilns
Cement is produced by heating a blend of limestone and clay in a kiln. This process releases CO2 as limestone decomposes. It is also energy hungry — the chemical reactions involved require temperatures as high as 1,500 °C. Most kilns run on fossil fuels and have poor thermal insulation.
What’s the best way to tackle climate change? An ‘evidence bank’ could help scientists find answers
Upgrading kilns can save energy and reduce carbon emissions. For example, over the past few decades, much of the world has moved away from vertical shaft kilns, which work much like a blast furnace — material is added at the top of the column and this is heated from below using gas or coal, to eventually form the cement component clinker. These are being replaced by rotary kilns, which feature a horizontally inclined, rotating shaft that helps move materials through the kiln.
Rotary kilns outperform shaft kilns in terms of production capacity, product quality and operational flexibility, and can process 60 times more cement than the average shaft kiln. Their energy efficiency can be improved by 20–50% by using technologies that conserve or recover waste heat3. Improving insulation and optimizing operations using computer modelling and real-time data can increase the efficiency further.
To make kilns even more efficient, next-generation technologies are being explored. These include all-electric kilns and ones that suspend raw materials in hot air to speed up reactions. Renewable energy sources, including solar, wind and biomass, as well as hydrogen, can be deployed, as can carbon capture and storage technologies to lower carbon emissions. Leading Chinese cement manufacturers, including Anhui Conch Cement, China National Building Material and China Resources Cement, have established next-generation technology pilot projects.
Use less clinker
Reducing the amount of cement clinker used in concrete can also bring down emissions. Some of it can be substituted with materials that require less energy to produce, including industrial by-products such as fly ash from coal combustion, ground blast-furnace slag from iron production, and recycled powders derived from materials such as glass, brick and concrete.
We need to prepare our transport systems for heatwaves — here’s how
However, current standards in China (GB 175-2020) and Europe (BS EN 197-1 2011) only allow up to 20% of the clinker in commonly used types of cement to be substituted by ash and slag. There are ways to replace more of it, while maintaining performance in construction. Updating these standards to reflect ongoing technological advancements is essential to widen adoption.
In limestone calcined clay cement (LC3), half of the clinker is replaced with a type of clay and a combination of limestone and gypsum, which cuts CO2 emissions by 40% while maintaining the required physical properties4. Major cement manufacturers, such as the Swiss firm Holcim and Germany’s Heidelberg Materials, have already adopted this technology; it is used in the Swiss embassy building in New Delhi, for example.
Moving forwards, it is essential to understand better the properties of various clay sources and to optimize their processing to ensure homogeneity and stability. Long-term durability studies need to be conducted across diverse environmental conditions. And large-scale trials are needed to address manufacturing challenges. Developing standards and increasing awareness among stakeholders is crucial.
Use less cement
Reducing the proportion of cement paste in concrete is another strategy. Conventional concrete typically contains about 30% ordinary Portland cement paste by volume. Using less can make concrete harder to work with as it becomes stiffer. But research on optimizing the packing of concrete particles indicates that the volume of paste can be reduced to 18–20% while maintaining performance.
The world must rethink plans for ageing oil and gas platforms
The ultra-green concrete5 project, announced in 2023 and supported by the Swiss National Science Foundation, has set an ambitious target to reduce the paste content even more, to as low as around 13% by volume. This goal relies on the material having a dense particle structure, known as advanced high-packing, and the incorporation of materials, such as modern superplasticizers. Challenges to overcome include the entrenched misconception that using less paste will affect the concrete’s strength and ensuring that this close-packed concrete meets practical tests, including durability and workability.
Advances in big data, machine learning and artificial intelligence can also play a part in designing more-sustainable concrete. For example, producers mainly depend on the 28-day compressive-strength benchmark specified in current standards. Through computer modelling, researchers can identify other time points to guide concrete design.
Use less conventional concrete
Reducing concrete consumption by extending service life, optimizing the design of structures and using advanced construction technologies, such as 3D printing, offer other ways to reduce carbon emissions and material use.
Risks of bridge collapses are real and set to rise — here’s why
Concrete formulations can be tailored for specific projects to minimize the unnecessary consumption of concrete and its environmental footprint. Options include foamed concrete, or those including a high proportion of recycled content. Old concrete components can be reused by casting them in fresh concrete. And other materials such as fibre-reinforced polymers and steel sleeves can be incorporated to enhance structural performance while using less concrete.
Although constructing a building requires a lot of energy, clever designs that lower the amount of energy needed to run it once it is built can save more. For example, using lightweight aggregate, honeycomb structures or composite materials in concrete can enhance the thermal insulation of buildings, so that they can run with smaller and more efficient heating, ventilation and air-conditioning systems.
Photovoltaic technology could be embedded in concrete, although many research challenges remain, including optimizing their efficiency, quality control during manufacture, degradation, environmental impacts and end-of-use recycling. Advancing these technologies will require close collaboration between material scientists, engineers and architects.
Sequester CO2 in concrete
Concrete can be engineered to absorb and store CO2 during its manufacturing, curing, servicing and recycling stages. One study6 estimated that economically viable CO2 mineralization in concrete materials could mitigate up to 15% of CO2 emissions from cement clinker production, and theoretically almost 60% is possible.
The problem is that some CO2 mineralization technologies are still expensive compared with manufacture of conventional products and other carbon capture and storage methods. For example, producing a carbonated concrete block is around 35% more expensive than producing it with ordinary Portland cement, at a cost of €161 (US$166) to avoid one tonne of carbon emissions6. For now, this limits its use.