Researchers developing low-cost preventive maintenance system for UAVs
By DRONELIFE Features Editor Jim Magill
As more and more commercial drone operators build out their fleets of UAVs, and as those drones begin to experience normal wear and tear over the next several years, the need for preventive maintenances will grow exponentially.
A team of researchers at the University of Texas at Arlington is developing a low-cost system that uses millimeter-wave radar to monitor small fluctuations in the mechanical performance of unmanned aircraft to recognize potential problems before they develop in order to keep the drone fleets flying.
“I think this is a very promising solution, especially for very large systems with a lot of drones,” leading researcher Dr. Dianqi Han, an assistant professor in the Computer Science and Engineering Department at UTA, said in an interview.
Han said the millimeter-wave radar defect-detection system, which his team has successfully tested in lab settings, could be developed for commercial application within the next several years, just as the need for such a maintenance solution becomes more pronounced.
Currently most companies that operate drone fleets still rely on humans to manually check their vehicles as part of a regular maintenance program. Since widespread use of drone technology is a recent phenomenon and drone fleets still are relatively new, mechanical failure that leads to catastrophic consequences is infrequent.
“So, if the drone crashes, it just crashes, then they will just replace it, Han said. “As drone use becomes more common, it’s going to be more of a problem as far as maintaining these (UAVs), as they age out.”
The UTA preventive system employs high-resolution millimeter-wave radar to spot tiny mechanical irregularities in a drone’s mechanical operations — such as changes in propeller speed or unusual vibrations — before they lead to serious failure. The system can also identify potentially more serious problems, such as a weakness in the drone’s joint system, which can result in crashes or collisions with other aerial vehicles.
“Our goal is a lightweight, cost-effective solution,” Han said.
He said the team hit on the use of millimeter-wave radar, because a small radar unit can cover a very large area and can detect small anomalies from long distances away. Such a system can also capture fundamental information about a moving object, such as its rate of vibration, velocity and distance from the radar.
“When we looked at the drones, we found that actually most of the hardware malfunctions will be reflected in the mechanical characteristic of the drones, like the vibration of the drone body, the rotational speed of the propeller, and also the trajectory of the drones’ movement,” Han said. “And using the millimeter-wave radar, we can perfectly capture those features.”
He said the research team has completed its initial testing phase of the system, proving the radar’s ability to measure a drone’s velocity and vibrations from more than 100 meters (about 330 feet) away. In the next step of the research, the team will study how to associate those features with the potential for hardware malfunction of the drones.
The research, which got underway this month, is expected to conclude at the end of August 2026, at which time the team hopes to develop a prototype system to confirm its feasibility for use in real-world conditions.
Han said he sees the greatest value of such a preventive maintenance system will be for operators of large drone fleets, such as UAS delivery companies. “For most users with just one or two drones, of course, they you can just regularly check the drone device by themselves. It’s very easy,” he said.
One major advantage of a preventive-maintenance system based on the UTA research would be its low cost. The Texas Instruments millimeter-wave radar used in the school’s study can be purchased for about $300. Apart from the radar, the only other component needed would be a laptop computer to capture and process the data, making the entire system available for less than $600, Han said.
“That’s pretty cheap. And just the one site can cover a very large area and it can do the detection and do the diagnosis for maybe hundreds of drones at the same time,” he said.
Once the team develops a prototype system, a number of challenges remain on the road to commercialization, such as adapting the system to adjust to changes in environmental conditions, teaching the system how to deal with different models of drones, and developing a process to ensure that all drones being scanned remain within the sensing range of the radar.
Han said once the research reaches the prototype stage, the next step in development will likely be to seek funding from federal agencies and private companies to develop a plan for commercialization.
“If we can get funding to support our work, I think we should be able to have some technique for commercialization well within another one or two years,” Han said.
Read more:
Jim Magill is a Houston-based writer with almost a quarter-century of experience covering technical and economic developments in the oil and gas industry. After retiring in December 2019 as a senior editor with S&P Global Platts, Jim began writing about emerging technologies, such as artificial intelligence, robots and drones, and the ways in which they’re contributing to our society. In addition to DroneLife, Jim is a contributor to Forbes.com and his work has appeared in the Houston Chronicle, U.S. News & World Report, and Unmanned Systems, a publication of the Association for Unmanned Vehicle Systems International.
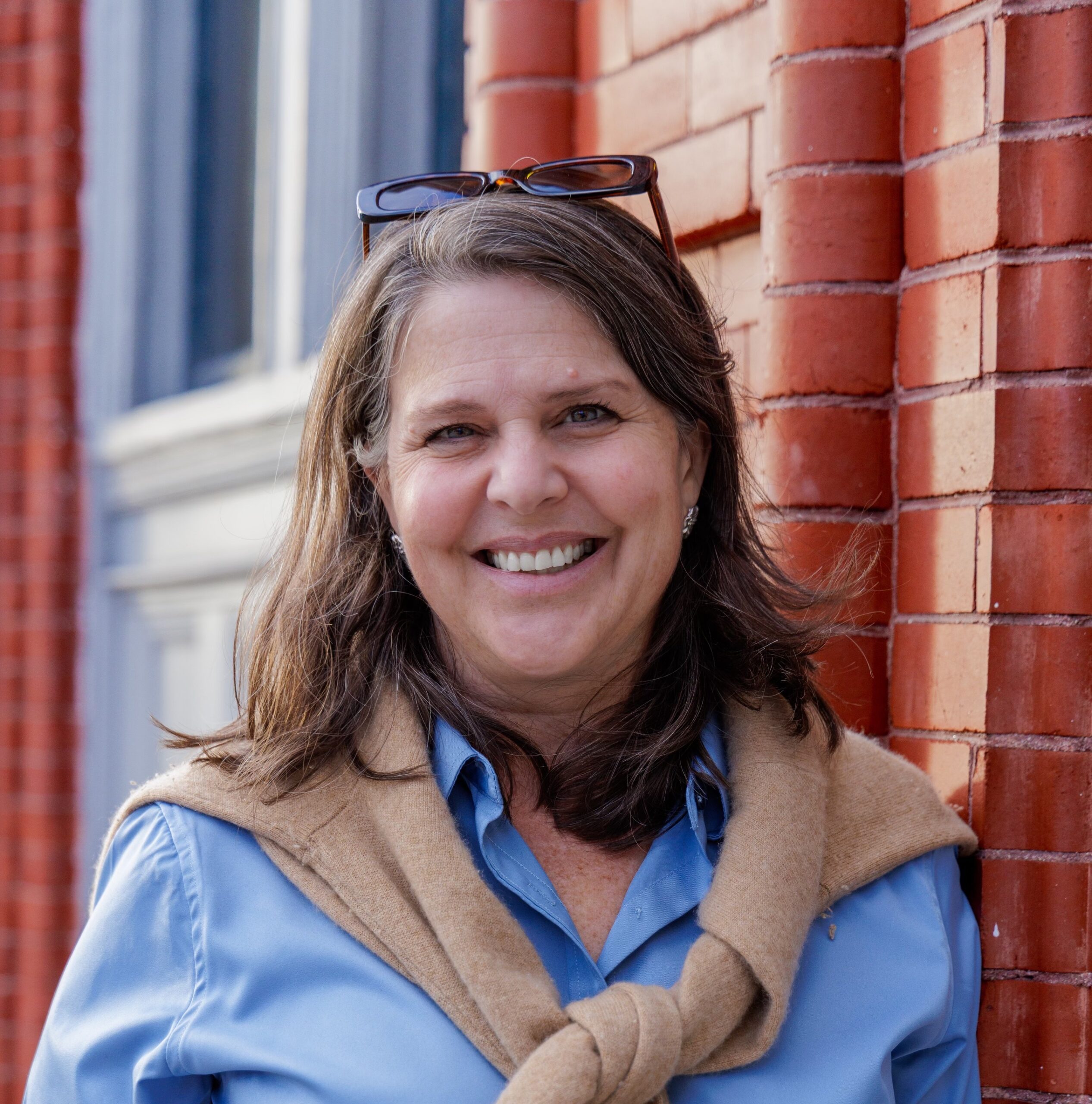
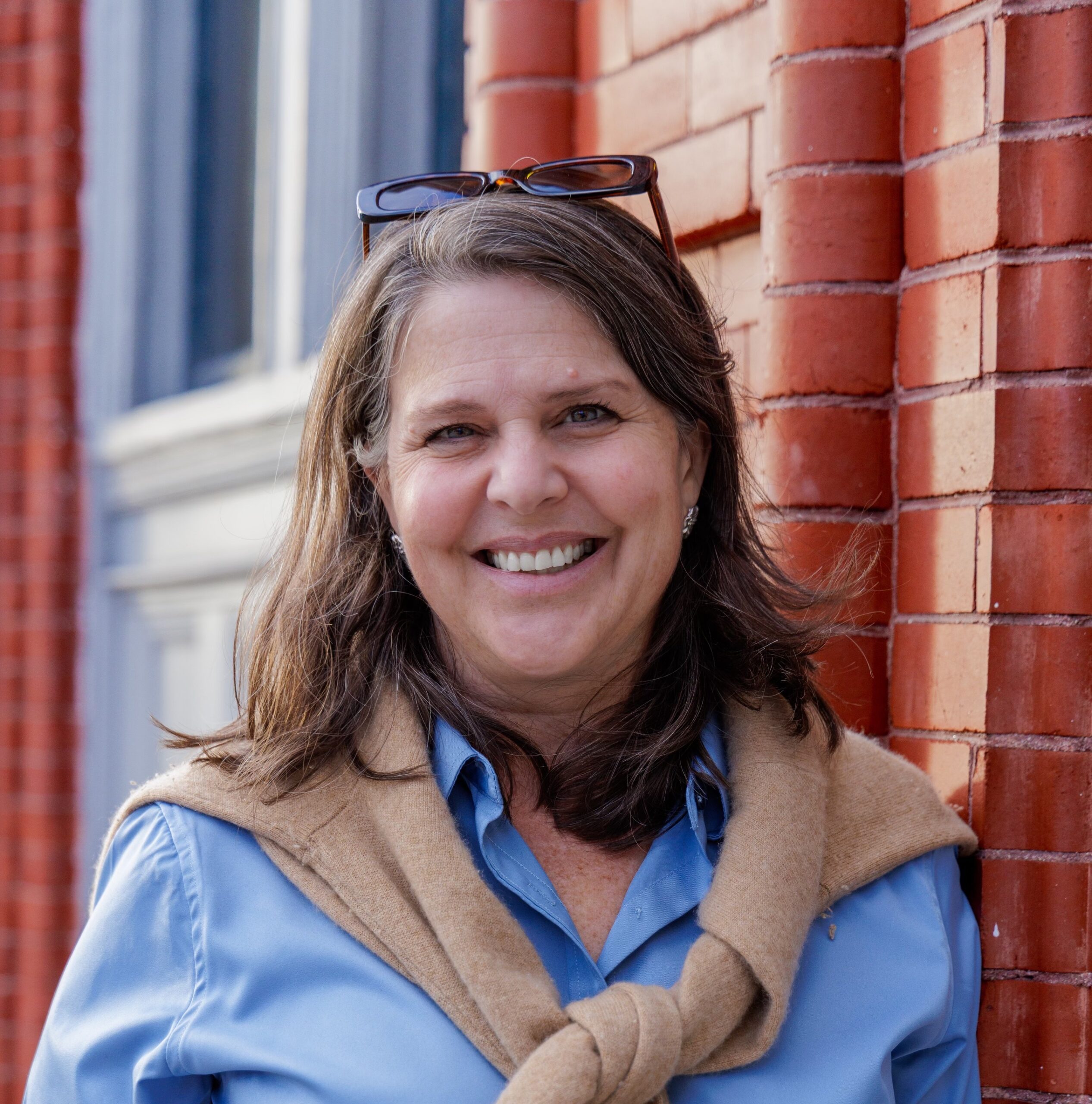
Miriam McNabb is the Editor-in-Chief of DRONELIFE and CEO of JobForDrones, a professional drone services marketplace, and a fascinated observer of the emerging drone industry and the regulatory environment for drones. Miriam has penned over 3,000 articles focused on the commercial drone space and is an international speaker and recognized figure in the industry. Miriam has a degree from the University of Chicago and over 20 years of experience in high tech sales and marketing for new technologies.
For drone industry consulting or writing, Email Miriam.
TWITTER:@spaldingbarker
Subscribe to DroneLife here.