The annual XPONENTIAL conference, hosted by the Association for Uncrewed Vehicles and Systems International (AUVSI), brought more than 7,500 global leaders and end users from over 60 countries to Houston, Texas, from May 19–22, 2025. In a panel discussion at Xponential, three US manufacturers explored how the United States can manufacture drones at scale- without relying on China.
U.S. Drone Manufacturing: Can It Scale Without China?
Moderated by DRONELIFE editor Miriam McNabb, the discussion featured Peter Fuchs of Ascent AeroSystems (a subsidiary of Robinson Helicopter), a MA-based manufacturer of coaxial drone systems; Nick Grewal of ePropelled, NH-based manufacturer of electric propulsion systems for unmanned systems; and Tobin Fisher of Vantage Robotics, a CA-based manufacturer of dual use UAS.
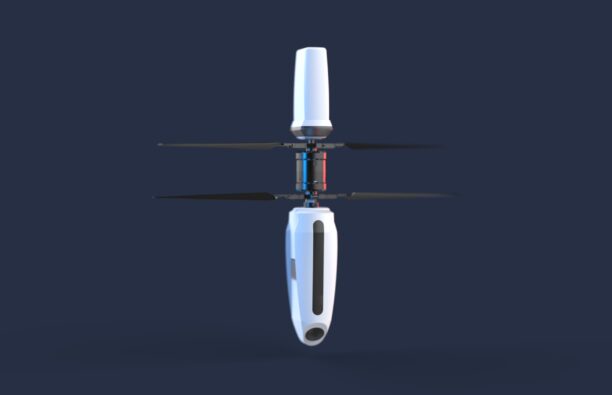
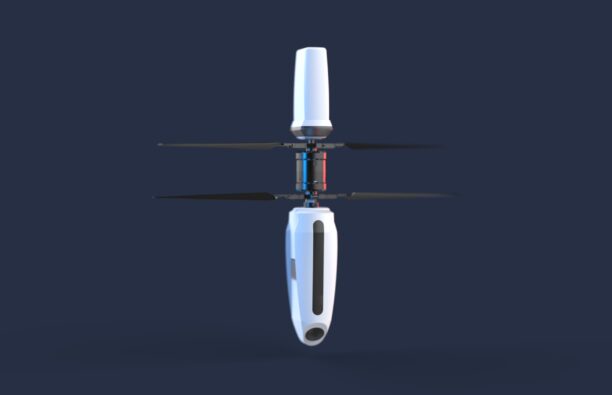
All three CEOs expressed strong confidence that large-scale U.S. drone manufacturing is not only possible but already underway. Peter Fuchs responded definitively: “Yes. It can be done. It is being done.” Tobin Fisher concurred, adding, “You have to be creative. You have to take unconventional approaches. Nick Grewal, whose company has been self-funded for more than 7 years, emphasized, “Yes…We are doing it now.”
Engineering for Simplicity: Reducing Human Input and Failure Points
One of the most important themes from the panel was that manufacturing in the US may not look exactly the same as manufacturing overseas. All of the three have engineered their products for simplicity and manufacturability right from the design phase. The panelists agreed that minimizing the need for human intervention is not just about reducing labor costs; it is also about improving quality and reliability. As Tobin Fisher explained, “Each place you need human input is a potential point of failure.” By designing drones with fewer assembly steps and less manual handling, companies can reduce both manufacturing errors and long-term maintenance issues.


For instance, Ascent AeroSystems’ latest micro Helius drone and Vantage Robotics’ Trace nano drone are both engineered with only six screws—a purposeful design choice to streamline assembly and minimize points of failure. This approach extends to ePropelled’s propulsion systems, where Nick Grewal described developing automated testing systems: “I tell my engineers, I want only two lights after testing. It’s a green light or a red light. That’s it.” This binary approach to quality control further reduces the risk of human error and ensures consistency across production runs.
Challenges: Demand, Competition, and Standardization
Despite progress in engineering and automation, the panelists agreed that insufficient demand from U.S. government and commercial procurement remains a major barrier to scaling domestic manufacturing. While there is strong advocacy for American-made drone platforms, purchasing volumes have not yet reached the levels needed to drive down costs and support large-scale production. Chinese manufacturers, with their lower prices, continue to dominate much of the market, making it difficult for U.S. firms to compete.


Standardization also emerged as a critical need. Currently, companies like ePropelled must manage nearly 100 different SKUs to meet varying client requirements, which limits economies of scale and complicates manufacturing. Greater standardization would simplify production, improve interoperability, and mirror the efficiencies seen in industries like automotive manufacturing.
Supply Chain and Rare Earth Metals
Establishing a robust, less China-dependent supply chain remains a work in progress. Ascent and Vantage source some non-critical parts internationally but prioritize U.S.-based assembly, testing, and critical components. Strategic stockpiling and parallel sourcing arrangements help ensure continuity, but the infrastructure for a fully domestic supply chain is still developing. “3D printing is just too slow for manufacturing at scale,” Fisher pointed out, highlighting the need for efficient, automated production methods.
A major concern is China’s recent restriction on rare earth metal exports, which are essential for drone motors and electronics. Grewal reported that ePropelled is actively developing relationships with alternative suppliers and that U.S.-based mines are rapidly coming online. “Customers are working with us to purchase necessary materials,” he said, saying that by taking a flexible approach the company is confident that they will be able to weather the current challenges.
Looking Ahead: Optimism for U.S. Drone Manufacturing
Despite these obstacles, the panelists remain optimistic about the future of U.S. drone manufacturing. They see progress in developing ex-China supply chains and believe that increased standardization, automation, and government support will help domestic manufacturers scale up and compete globally.