Last year, 21 teams of battery researchers from around the world participated in a benchmarking test. They were each tasked with constructing a solid-state battery using their own equipment and commercially available materials while following a standardized set-up procedure. Despite using the same instructions, the performance of the batteries, and process used to build them, varied wildly across the laboratories.
Fans of a well-known TV baking show might recognize this scenario. Each week, Bake Off contestants are given the same ingredients, equipment and recipe and their creations are judged against one another. Even though the bakers follow the same basic procedure, the results are often very different because key steps are left out of the recipe, including mixing techniques, oven temperature and baking time.
Reproducing research is not much different. In the battery benchmarking test, teams were left to come up with their own techniques using their preferred equipment and components to create the electrochemical cells that power their batteries. The basic set-up required two electrodes to be separated by an electrolyte, which helps to move electrons from one electrode to the other to convert chemical energy into electrical energy. The most common configuration among the test groups involved placing a solid electrolyte between two active electrode materials, all pressed together by two metal stamps. The pressure inside the cell changed based on the equipment used. When the batteries’ performance was tested, there was a huge difference upon first discharge, ranging between 21 and 143 milliamp-hours per gram of battery material — enough power to run small LED light for a few minutes versus a wearable fitness tracker for day or so.
Nature Index 2025 Energy
The team behind the experiment, led by Nella Vargas-Barbosa, an electrochemist at the University of Bayreuth in Germany, says the results emphasize the need for more standardization in battery research. In a paper published by Nature Energy1, the team recommends that future solid-state battery research specifies the pressures that were used in construction to help others reproduce the work.
The benchmarking exercise follows a similar study, run as part of a UK-based project called Nextrode. Five British universities were asked to independently construct electrochemical cells using the exact same method as each other. Various measures were taken to ensure that the teams were following the same steps and not influencing each other in any way, says Denis Cumming, a battery researcher at the University of Sheffield, UK, who oversaw the experiment. “We had everyone all over the country do this at the same time on the same day in a week” to stop teams passing on tips and tricks, he says.
The results are yet to be published, but Cumming says that the failure rate among the 120 cells that were built was high: many short-circuited or failed to charge and discharge properly. “It’s very difficult to standardize these processes — extraordinarily difficult — because there are so many variables,” says Cumming.
The problem isn’t just that there are several components within a battery that might have been made slightly differently and with slightly different properties. It’s often very difficult to access enough raw material of the same quality, Cumming says. He adds that even commercial materials can vary from batch to batch, and most labs don’t have the tools to measure that variability. As it stands, there are no standard methods that everyone in battery development abides by. There is no standard data set to compare results against, no standard way to build components, and no standard formulation for the materials that go into a cell. To bring these kinds of standards into the field will require somebody to do, and pay for, the work.
No standard
Battery research could learn from the field of bioinformatics, says Simon Clark, a sustainable energy researcher at Norwegian institute SINTEF in Trondheim. “When it comes to reproducibility, standardization and openness of data, bioinformatics was the field that adopted it very early on,” he says. In the 1970s, bioinformatics researchers increasingly made their databases open access and used standardized formats, says Clark, and by the 1990s, they’d started to have regular benchmarking sessions for work related to protein-structure mapping. So, when the team behind the AlphaFold artificial intelligence (AI) system, developed by Google DeepMind to predict protein structures, runs its program, “they don’t have to start from scratch”, says Clark.
Battery data, by comparison, have not been collated rigorously over the past 50 years, because the field has been built on the efforts of individual labs, each developing their own interests in either materials, manufacturing or fundamental electrochemistry, he says.
Clark was part of the Battery Data Genome, an international collaborative project launched in 2022 to improve data collection, sharing and standardization in battery research through open-source tools and best practices. In a paper published in Joule2, which set out the principles of the project, the authors recognized that it would take time for the research community to accept their ideas, but argue that change is urgently needed if the clean-energy transition is going to happen. “The risk is not in moving forward, but in staying as we are now,” they write.
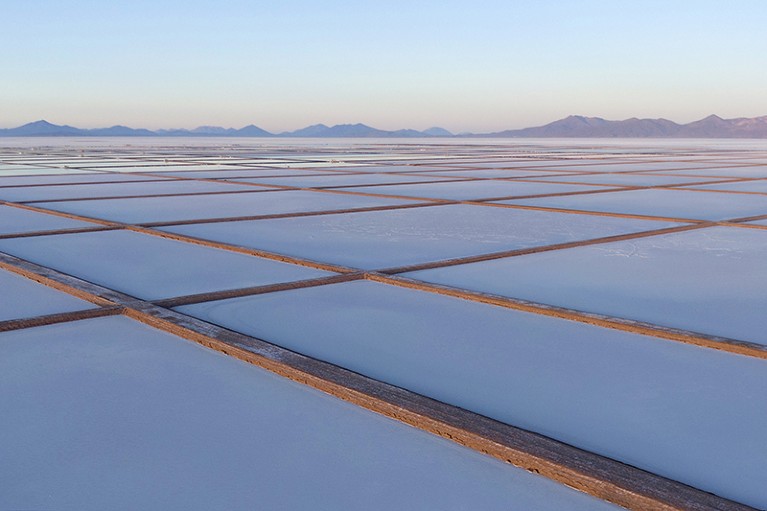
Salt recovery pools at a lithium plant in Bolivia. Lithium is a significant resource in battery development.Credit: Gaston Brito Miserocchi/Getty
Other battery researchers are feeling the pressure to make the field more robust. Europe’s Battery2030+ and the UK’s Faraday Battery Challenge, for example, which link up research institutions, industry and public funders to develop better batteries, emphasize the importance of common protocols and methodologies to ensure consistency, safety and efficiency across the battery industry.
This is also a key focus of Battery500, a consortium of 14 national laboratories and universities in the United States that aims to identify the most promising battery materials and accelerate their commercialization. As part of the project, researchers at the Pacific Northwestern National Laboratory in Richland, Washington, where Battery500 is headquartered, have developed standardized protocols to test each component of a battery during construction.
The consortium has also set parameters for the optimal amount of electrolyte; the optimal amount of active material, such as lithium, to be applied to the cathode; and the optimal thickness of the lithium foil3. Papers that report these parameters have been cited hundreds of times, suggesting that other researchers are following their lead and applying these protocols to their own systems.
The publishing world can also help to promote standardization. In early 2021, Joule introduced a battery checklist that researchers who want to publish battery performance results in the journal must complete. “When I was a graduate student working on lithium-ion batteries, I would often find myself deep in the supplemental information section of papers, searching for experimental details that would allow me to replicate an experiment,” Alexandra Stephan, then an editor at Joule, wrote in an editorial about the checklist4.
Stephan notes that key details such as electrode composition would sometimes be missing from a paper. “It was an incredibly frustrating experience,” she writes.